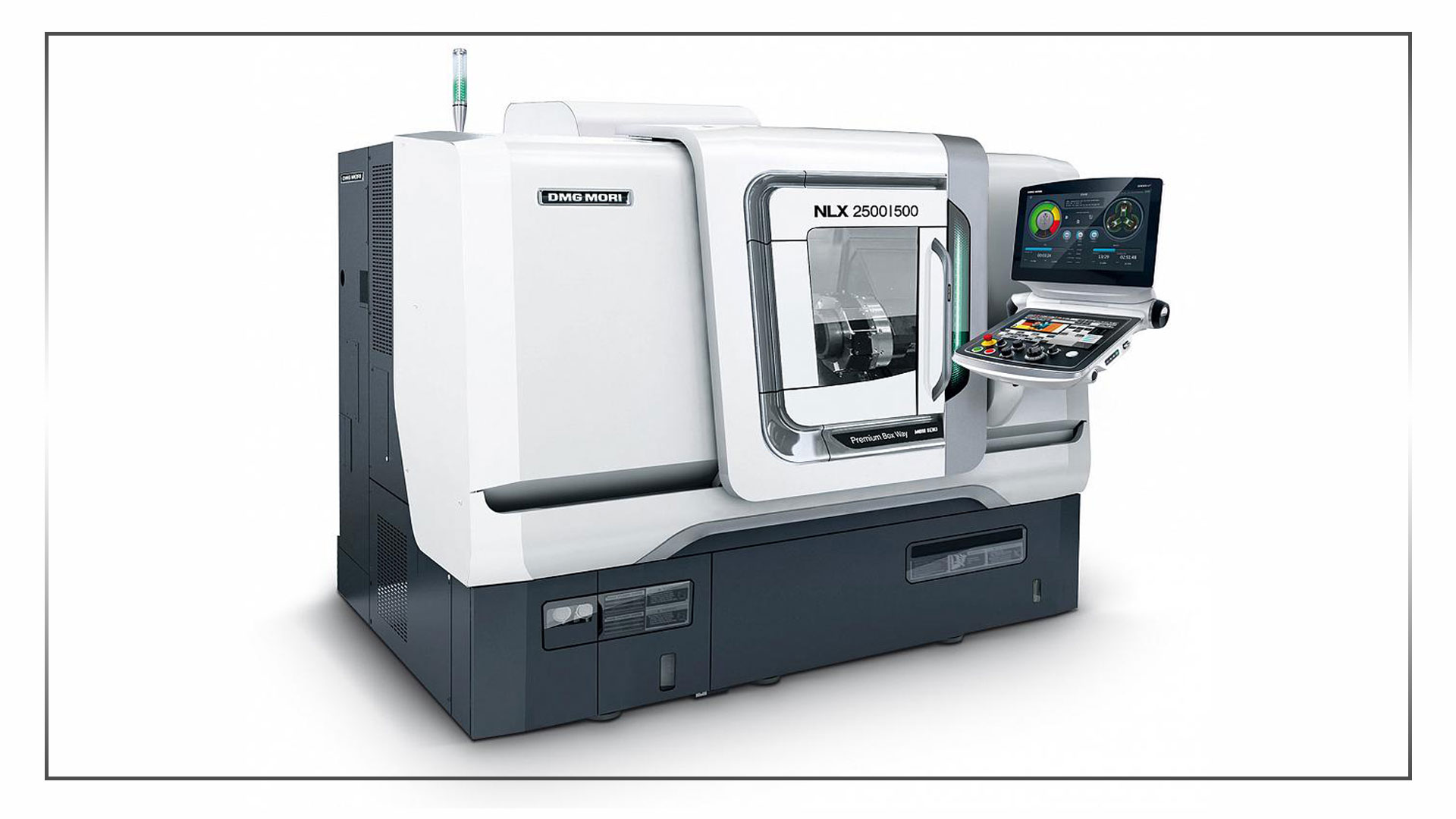
You can receive your machined deliverables on time, on budget, and crafted to perfection. All you need to do is choose the right shop with the right equipment!
Lathe-turned deliverables are a specialized product. Finding the right machine shop partner is often challenging for business owners. In your search for the right supplier, you may find yourself dealing with missed deadlines and inferior deliverables.
Time is money. To succeed in the modern marketplace, you must find and work with a machine shop that enables you to make the most of your time.
Today, you don’t have to settle for less, such as reducing weight by forfeiting durability.
Machine shops that use the latest in machining tooling can deliver great-looking products. They can also reduce turnaround time. They do this by using advanced machinery designed to streamline the manufacturing process.
Leading machine shops can handle high-capacity jobs, starting with raw stock that can range from 12 to 20 feet in length for the biggest jobs.
Companies across a range of industries outsource lathe-turned metalwork jobs, from the automotive to medical industries. The latest versions of metalworking equipment have made it easier for machine craftsmen to execute complicated builds.
Today, lathe-turned metalwork shops produce high-quality goods at reduced costs. Furthermore, they can provide those benefits no matter how complex the project.
Craftsmen must perform additional machine work on nearly 70% of all projects. Of those projects, they could save this additional step by completing the project using a Y-axis machine.
In the most basic sense, Y-axis metalworking equipment simply streamlines production. They’re more about integrating workflows than technology.
Compared side-by-side, there’s no contest between a single the mill and Y-axis machines.
In recent years, the look and feel of top machine shops have changed. They’ve learned to create better-quality deliverables faster.
Now, machine shops can deliver smaller lots, reducing the chances that you’re left with excess inventory. This circumstance is a significant change from the days when machine shops used standard milling machines.
In the past, a machine shop would complete your project in steps. In the end, they would deliver quality goods, although on a longer timeline.
Now, features such as automatic tool changers enable machine shops to combine processes. It’s more common, for example, for a metalworker to work with a machining center, rather than separate milling tools.
Because of this, progressive metal cutting steps are a rarity in leading machine shops. This transformation has enabled machine shops to deliver better products faster.
A machining center reduces most of the physical movement involved in manufacturing goods. Now, workers can build your order to spec in a single operation.
There’s no longer a need to set up multiple machines. Skilled machine shop workers can now set up your job in a single handling.
With the addition of the Y-axis feature, more machine shops have gravitated toward a single setup workflow. The limitations of the time-tested four-axis lathe is unavoidable for many jobs.
There are techniques, such as polar coordinate programming, which try to make up for the shortcomings of four-axis lathes. Still, this method can’t compensate for the lack of a fifth axis.
For example, there’s no way to drill holes in the corners of a milled cylinder flat without a Y-axis. Machine shop workers cannot access the edges of the flat without it. The Y-axis expands linear motion by 33%.
It helps to think of a Y-axis lathe as two machines in one. The equipment has a turning center, the same as a four-axis lathe. However, it also features a five-axis machining center.
Contemporary machine shops now use automatic loadingers that are pieces of equipment.
They also make use of roller tables. The tables make loading and unloading convenient.
They lessen the friction between the worktable and raw materials. They also feature intelligence assistance.
Leading machining centers also use Wi-Fi to collect and analyze projects. The technology enables machine shop supervisors to troubleshoot problems right from their office.
Today’s machine shops have also improved equipment maintenance. For example, cutting-edge lathes feature automatic lubrication systems. The systems reduce downtime and delivery delays.
Top machine centers also alert workers when it’s time to replace worn out parts. Machine center systems also monitor and alert workers about product abnormalities.
As a result, the best machine shops can do a better job maintaining quality control. If a problem arises, an alarm sounds, enabling workers to correct issues before they can slow down production.
The latest lathe technology enables workers to make close tolerance and high-quality parts, and they also eliminate much of the costs associated with manual lathe or just a 4 axis lathe.
Laser cutting enables machine shop workers to deliver on complex specifications. It makes production and assembly easier. It also makes it more cost-effective.
These advanced features have transformed the workflow of machine shops.
Today, it’s essential that you find a lathe service that’s more than a vendor.
You need a partner in business. A partnership will give you the advantages that you need to succeed in today’s competitive marketplace.
Once you’ve found a competent machine shop, you must work to build an authentic relationship with that company. A top machine shop displays transparency and honesty. They’ll put real effort into creating a working relationship that will help you to succeed.
Contact All Metals Fabricating today at (972)-747-1234 and experience the benefit of cutting-edge lathe-turned metalwork!