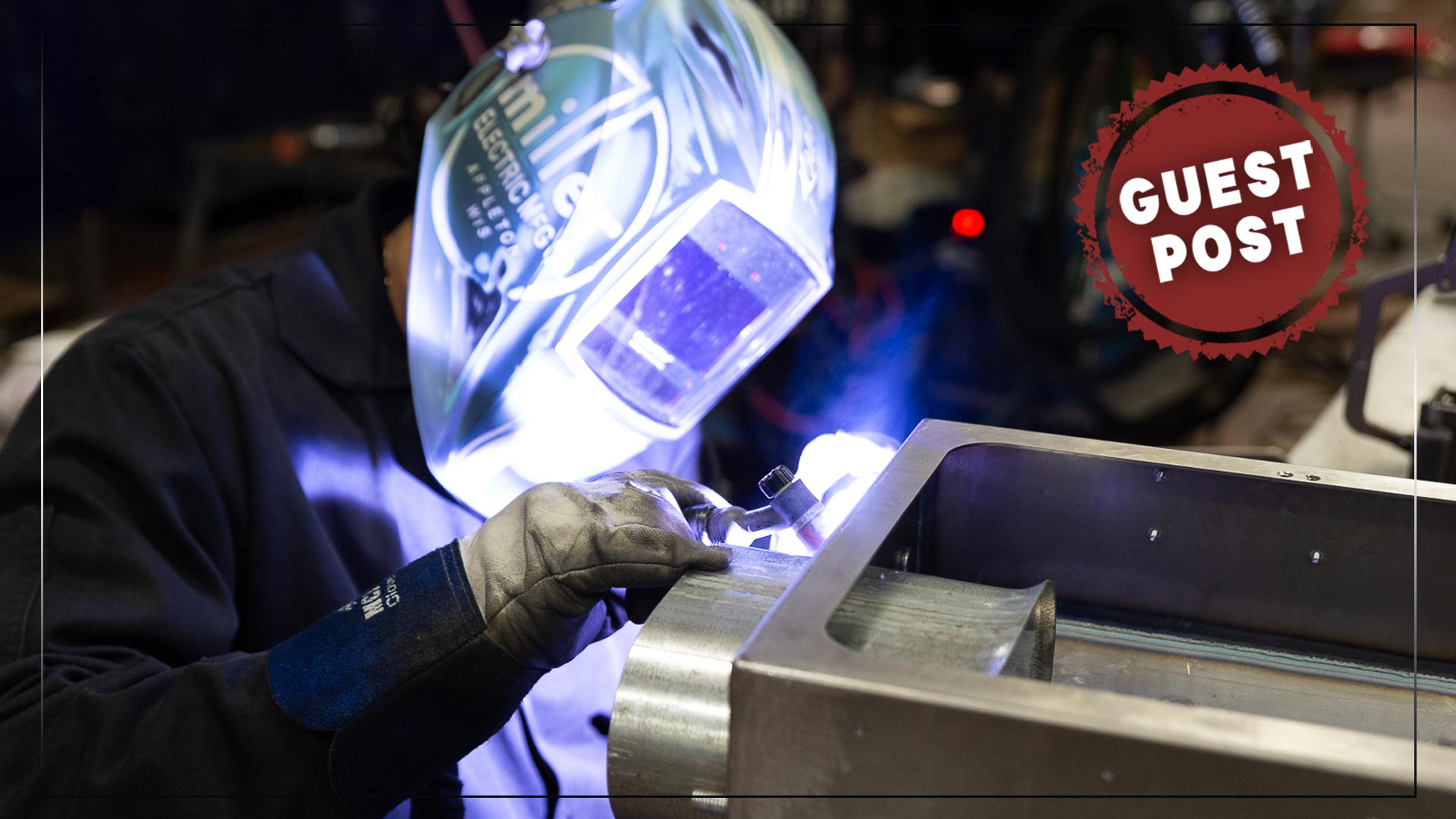
Manufacturing commonly uses production welding as a means to get certain jobs done. Since welding is a key component in building many of the products that are manufactured around the world, AMF has employed welders with a high level of experience and expertise to handle even the most demanding welding needs.
Since there are many different types of welding, it can be helpful to understand what each one does. So, we've created this article to help you discover the world of welding and all that there is to know.
Read on to find out more.
Welding is a process that involves joining two pieces of metal together. Unlike soldering or brazing, welding is conducted with the use of extreme heat, which is what joins the metal together.
During the welding process, it is common for other metals or gases to be added to create a structurally solid bond. Companies like a machine shop or a contract manufacturer rely on welding for their everyday business.
There are many different types of welding. Yet, there are a few that are most common.
The first type of welding that is common is Metal Inert Gas. This type of welding is also known as Gas Metal Arc Welding or MIG. How this welding process works is with the use of a thin wire acting as an electrode.
What happens next in this welding process is the wire will heat up as it is being fed through the welding equipment, towards the welding site. It is important to note that shielding gas can protect you from airborne contaminants when using this form of welding.
Of the many different types of welding, this one is widely used in automotive and construction. Gas Metal Arc welding has a reputation for being one of the easier types of welding to learn. So, if you are a beginner welder, then this would be a great starting area.
Another common type of welding is shielded metal arc welding or SMAW. With this form of welding, the process is slightly different. It depends on a manual technique to complete the welding process.
Shielded metal Arc welding uses consumable electrodes coated in flux. This type of welding is also more common in small welding shops. You can also refer to it as stick welding.
Shielded metal arc welding is a lower cost option than other forms of welding. The reason is that there isn't a lot of extra equipment required when performing the welding.
Unlike gas metal arc welding, shielded welding doesn't need a shielding gas. You can do this type of welding outside in adverse weather conditions such as wind or rain.
Shielded metal arc welding may not produce the most quality products. This is because it can crack, making it less durable.
Another type of common welding is Gas Tungsten Arc welding which is commonly referred to as TIG. This welding process uses thin materials that are non-ferrous to weld together. It is perfect for welding copper, lead, aluminum, or nickel.
Gas Tungsten Arc welding is very essential to plane manufacturing. How TIG works is it uses non-consumable tungsten electrodes to form a weld. In order for this type of welding to happen, you have to use an external supply of gas.
The gas that is needed to weld using gas tungsten arc welding is argon or helium mixed with argon. This form of welding is for more advanced welders as this is the most difficult. Yet, it produces welds with the highest quality due to the skill needed to complete it.
The last form of common welding is known as flux-cored arc welding or FCAW. While this form of welding closely resembles the processes of metal inert welding it does have a subtle difference. Flux-cored arc welding involves a continuous wire feed type of process.
This type of welding also involves a combination of processes to complete the weld. The first process is the use of shielding gas. While the second process depends on self-shielding agents produced when there is a fluctuation of agents decomposing within the wire.
This is also an easy-to-learn and inexpensive form of welding. Flux-cored arc welding can also be done outside and it is most commonly used in construction projects.
Welding is essential to so many industries. Without welding, there are many things that would not simply exist. For example, cars, buildings, even some kitchen appliances, could not operate without some form of welding.
Welding is important for production because of the way it is used. It supports the efforts of manufacturing and sheet metal fabrication. Welding is also used to take raw materials and transform them into things you can use on a daily basis.
There are several emerging trends in the welding industry. One of the most prominent trends is the implementation of automation. Robotics welding uses automation to enhance the performance of welds.
Not only does automation in welding increase speed and skill, but it also reduces errors compared to human welders.
Another trend that is emerging in welding is the lack of new talent. There are more welders retiring than those who are entering the field. This could signal a shortfall of welders in the future.
One other trend that is emerging in welding is safety. Welding safety has become a top priority for many manufactures. Companies are actively seeking new ways to remove hazards and protect their employees from accidents.
Welding is a crucial factor in production, machining, and manufacturing. You want to trust experts who can get the job done right. With years of experience and quality customer service, we are here to help with all your welding needs.
Contact us today to get a free quote and let the experts help you with all your production requirements.