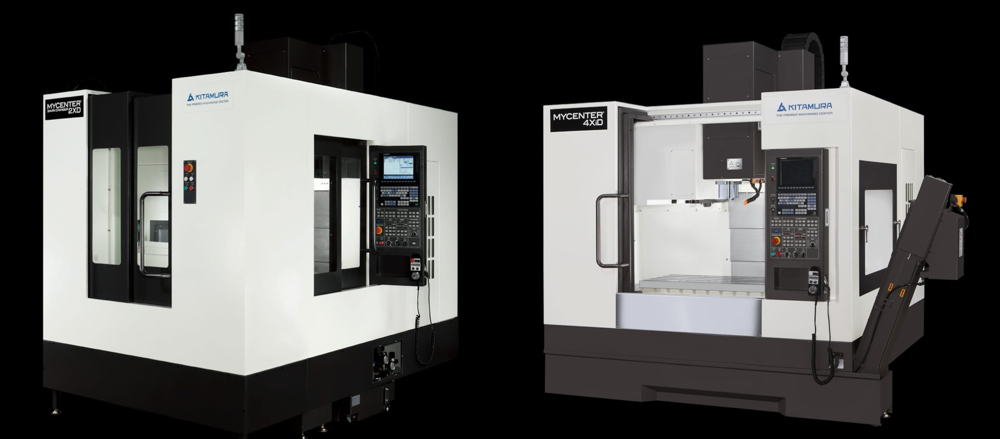
Two years ago, All Metals Fabricating was one of the first contract manufacturing shops to implement Alora, an advanced machine monitoring system. As always, our goal was to serve our customers better, but we didn’t realize just how valuable this new technology would be.
Fast forward to 2023: Since implementing a machine monitoring system, we’ve increased our machine utilization by 152% on our day shift and output by $275,000 annually, without even factoring in the additional output from lights out manufacturing afterhours. We estimate at least the same amount of increase, if not more, on the light out production increase. Best of all, a higher level of productivity helps us improve costs and lead times for our customers.
Machine monitoring systems like Alora measure how often our machines run and track planned and unplanned downtime. This software gives our team precise insights into where and how we can improve our process.
We didn’t make any changes for the first month after the software was installed to set a benchmark for how our shop operated before machine monitoring.
Two years later, we're benefitting in four key ways:
Our team quickly realized that some machines were not operating close to 100% of their potential.
We’d been considering buying a new laser cutting machine because of slow output, but Alora revealed that our utilization of the machines we had was under 40%. Instead of spending nearly $2 million on a new machine, we used Alora's data to improve our current machines' utilization.
But it’s not just the laser cutting department that’s improved. After two years of informed decision-making based on our machine monitoring data, our productivity has reached an all-time high across the shop floor.
Here are just a few of our improved metrics:
Machine monitoring increased our machine utilization by 35%, added nearly 50 hours of machine operating time per week, and boosted our output by $275,000 per year.
With machine monitoring, we can make adjustments to increase productivity while a job is still on the shop floor.
If an operation takes much longer than anticipated, we use Alora to see what the machine was doing at that time, if there were significant gaps in downtime, and the cause of the downtime. Then, we can immediately adjust to improve productivity for the next operation.
One of the most significant benefits of machine monitoring is our ability to track machine utilization during lights-out machining. Before installing Alora, we had to rely on our camera system to review major problems. Now, we have an entire dashboard dedicated to tracking the utilization during lights-out machining.
Machine monitoring has introduced radical employee accountability to our shop floor. Department leads receive a weekly report with metrics from the previous month, and the entire team reviews it to find tangible ways to improve their process.
In one of these meetings, the machine shop department reviewed the data and suggested adding an extra tooling cart and standardizing some tool setups. These small changes are easy to implement and boost productivity.
Our machine monitoring software also helps incentivize individual employees to maximize their efficiency. As many industry veterans know, precision sheet metal fabrication is a repetitive job, and machine operators can struggle to stay motivated. Alora gives each employee a personalized dashboard measuring their quarterly performance. AMF adds incentives by providing a $500 bonus to employees who exceed their goals.
We’ve seen increased employee engagement thanks to machine monitoring, which leads to higher-quality parts and better productivity.
After two years of implementing machine monitoring, our productivity increases at an individual machine level have begun to level out. We can now focus on proactively improving our machine shop and sheet metal fabricating productivity by examining the data accumulated over the past two years.
With Alora, we can see which machines are clocking more downtime and review the programming to see what might be causing the problem. Similarly, if a machine is breaking down more often, we can find out why and find additional opportunities for preventative maintenance.
Ultimately, information is power. Machine monitoring gives the AMF team unprecedented insight into what’s happening on our shop floor, empowering us to find solutions before the problems grow large enough to impact productivity.
With just one investment, AMF increased our productivity by 152% and continues to save customers time and money. But our mission of continuous improvement doesn’t end with machine monitoring.
AMF will continue to invest in state-of-the-art machines and innovate our processes to provide the best possible service to our precision sheet metal fabrication customers. We refuse to settle for “good enough” because we know we can do better.
Request a quote today.