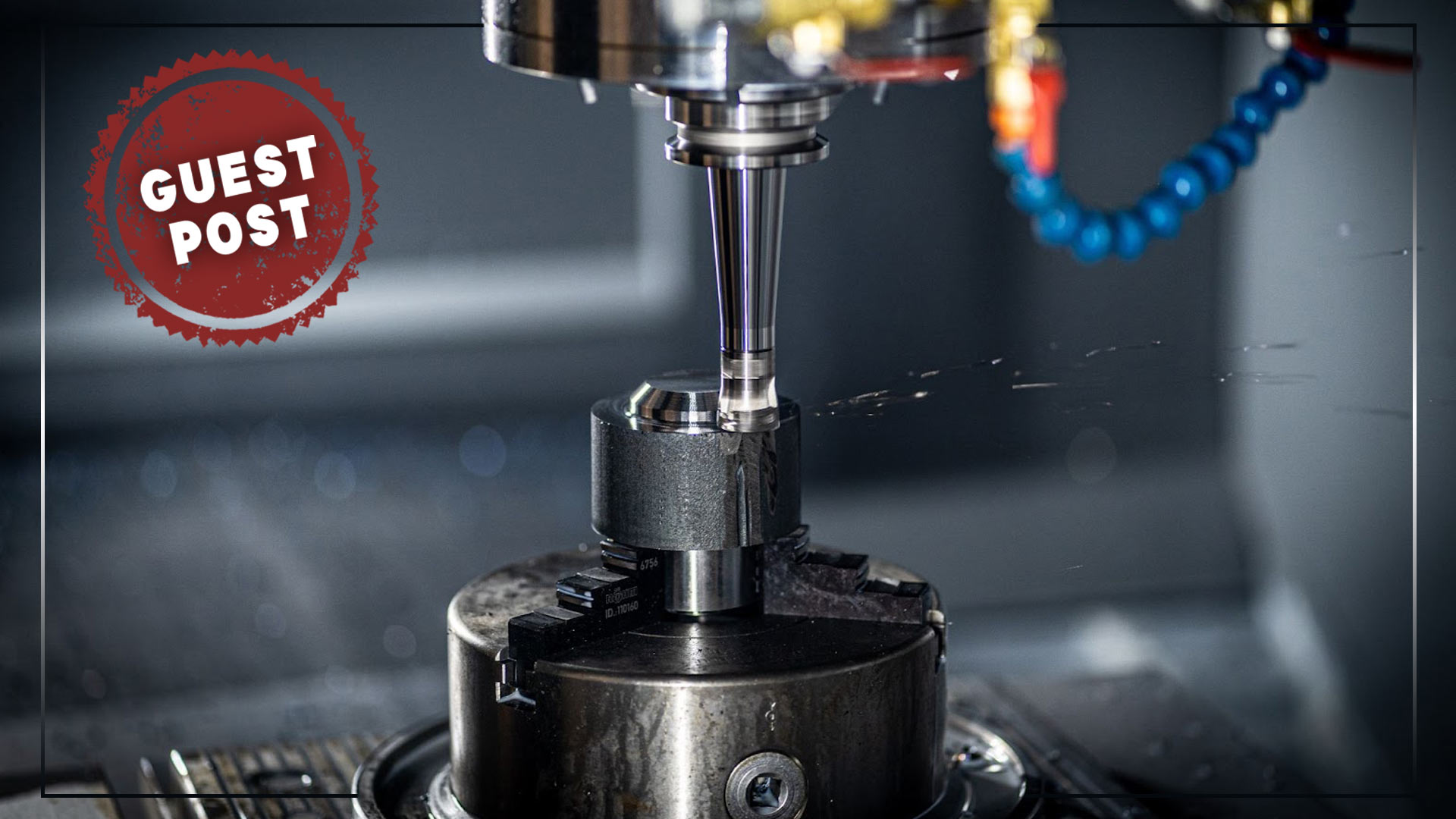
Last updated April 2025
The sheet metal fabrication industry has evolved significantly since da Vinci’s first sketch of an early sheet metal technique in 1485. Today, it is a critical manufacturing process for sectors such as aerospace, construction, energy, and automotive.
Modern metal shops are more advanced than ever, leveraging cutting-edge technology and automation to improve precision and efficiency. In this article, you will learn what metal fabrication is and how the process works.
You use many products daily that are staples of the metal fabrication sector. Mailboxes, roof gutters, phone casings, and air-conditioning ducts/furnace flues are all examples.
Most metal fabricators work with sheet metal. Sheet metal fabrication transforms raw sheet metal into a variety of finished products. Sheet metal is available in standardized gauges and materials, making it suitable for both mass production and custom products.
Metal fabrication uses complex machinery and manufacturing processes to manufacture high-quality products. Sheet metal typically arrives from a wholesaler or metal mill for a fabrication process that can include cutting, folding, forming, bending, engraving, and more. Standard tools that a metal fabricator will work with include lasers, punch presses, and press brakes.
When high-quality products require clean cuts and no discoloration, a laser cutter will often be used. Intricate patterns are another critical use case for laser cutters. These machines are valued for their ability to handle a wide variety of metals, including carbon steel and titanium.
Metal fabrication involves many different material options, and the proper choice can be critical to project success. For instance, more than 3,500 different grades of steel exist, over 75 percent of which have been developed in the last twenty years. It’s important to partner with an expert fabricator who can guide you through this complex decision.
Product engineers start the process by sending out plans and sketches to different fabricators to get quotes. The fabricators come up with a cost estimate and timeline based on their experience and the potential project.
From these quotes, product engineers select one fabricator for that particular end product. Some end products can have several different fabricators involved in different elements. The fabricator then orders materials for the project, typically sheet metal, bars, rods, and tubes.
Once the parts arrive, the fabricators begin to work. For custom metal fabrication, the fabricators may play a role in the design process, as unique products need specific techniques to achieve the right result. Highly skilled sheet metal shops like All Metals Fabricating can offer excellent guidance on optimal fabrication choices, including design for manufacturing advice to ensure an efficient, cost-effective manufacturing process.
Sheet metal fabrication often integrates with other manufacturing processes, such as precision machining, when specific features require milling or turning. Common machining options include CNC mills and lathes.
The final step of the manufacturing process involves assembly and finishing. These processes prepare the product for use, whether with joining techniques or coatings. Methods like graining with a belt sander or applying a vibratory sanded finish are two raw metal finish options. Other common finishes include powder coating or various plating specifications.
The process of metal fabrication involves a variety of equipment, some of which are unique to metal materials. Here are a few examples of sheet metal services and equipment that can be involved in a project:
Precision sheet metal fabrication is a highly skilled and potentially complex manufacturing process often employed for high-quality products. Below is a short list of essential reasons why metal could be the right choice for your manufacturing project:
The final appearance of your product is critical. Many high-quality manufacturers, such as tech companies, have opted for a metal design. Metal gives smartphones and computers durability and a modern, sleek look.
Your product application demands durability. The durability of metal products is naturally superior to plastic. Notably, metal can withstand higher temperatures. If the manufacturer has taken into account expansion under heat, the heat will usually not damage the product.
Especially in high-volume manufacturing, metal fabrication is far more cost-efficient than other processes. Process replication can reduce the manufacturing cost per unit. Sheet metal fab is also more versatile, allowing for a wider variety of approaches. Options such as contract manufacturing or lights-out manufacturing can further improve a project’s costs, and many shops are investing in automation to increase efficiency.
Precision fabrication is a complex manufacturing technique, but it is highly versatile and adaptable. With the right fabricator, the process can result in a cost-effective, high-quality custom product.
Custom sheet metal fabrication is flexible, as well. Still, some processes will not work with certain materials or may be limited by product design. Therefore, it is crucial to contact a professional metal fabricator for advice and guidance during the design process.
If you’re ready to collaborate with us on your next sheet metal project, request a quote today!